18个小时!一辆长安汽车“从无到有”
记者 白麟
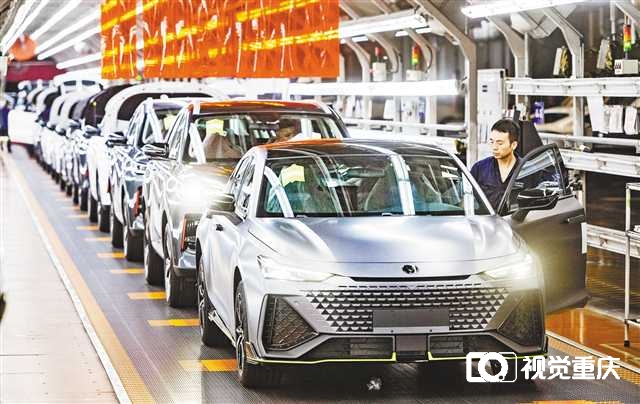
8月11日,长安汽车两江工厂总装二车间,完成涂装等工序的整车在这里进行最终的外观检测后正式下线。记者张锦辉摄/视觉重庆
一辆汽车有上万个零件,在主机厂的生产要经历冲压、焊接、涂装、总装四大制造工艺,流程极其复杂。不少人很好奇,生产一辆这样的汽车,到底需要多长时间?
最快仅需18个小时!
这是长安汽车给出的答案。目前,长安汽车的工厂智能化水平已处于国内领先。
这些制造工艺流程是怎样运作的?记者来到了长安汽车两江工厂实地探访。
上午10点 还是一堆车身板料
8月10日上午10点,记者步入两江工厂冲压二车间。
左手边的立体仓库里,一张张车身板料整齐堆放着,不久之后,它们就将被冲压成型,成为一辆汽车的车身外壳。
离仓库不远处的冲压线上,国内最先进的5台高速全自动冲压机,正以每分钟15次的节奏不停运转。一张板料从线首输入后,上到对中台,一只智能“光电眼”会主动对其进行准确定位,然后将其送到冲压模具“嘴”里,拉延、切边、整形、冲孔、翻边……一顿操作下来,一块车身零部件就成型了。
令人惊异的是,这整个过程都是全自动化,各种机器完美配合,有条不紊地自主运转着。
来到冲压线的另一头,记者终于看到了一个生产人员的身影,他正独自站在自动化总控台旁,盯着屏幕上数十个画面,上面显示着各个关键生产环节的情况。
冲压二车间高级经理张合礼介绍,该车间可以生产91个汽车零件品种,“我们什么时候生产哪一种零件,用哪一种原料和冲压模具,冲压的流程的设置,全部都是智能化、自动化的,实现了‘一键操作’”。
正说话时,只见刚才的操作员在总控台上按下一个按钮。生产线旁的红灯亮起,整条冲压线安静下来,暂停运作,开始更换冲压模具。根据厂里的生产计划,这条生产线将调整为生产第二代CS55PLUS引擎盖板。
五个长方体的“大家伙”——CS55PLUS引擎盖板对应模具,已通过桁架调运到预设位置。操作员再按下一个键,所有模具进入冲压线并安装锁定,冲压线又开始运作起来,整个换模过程不超过3分钟。要是过去的普通生产线,仅换模这一项,就需要好几十分钟时间。
张合礼说,冲压线生产一个车身零部件只需要几秒钟,但一般都会提前批量生产大量部件以备用,而后面的焊接、涂装、总装则是“一气呵成”,中间没有任何停顿,整个流程最快只需要18个小时。
下午5点 车身成型
比起冲压车间厚重、稳定的“气质”,两江工厂焊接二车间则如同“机械森林”般丰富和热闹。
“机械森林”由几百台机械臂组成。它们有的专门负责点焊、弧焊,有的则负责抓取,还有检测机器人和刻字机等。所有的机械臂都在不停舞动着,焊花按照精确的节奏,一朵接一朵地绽开。
上午11点,冲压车间此前生产出来的CS55PLUS引擎盖板,由无人物流小车送到了焊接二车间。在这里,一个个车身零部件被焊接、扣合成为稍大一些的模块,又再次被组合成为机舱、前后地板、底盘……最后,所有的零部件被组装为一个完整的CS55PLUS白车身。
焊接二车间高级经理孙建军介绍,在智能化技术加持下,该车间自动化程度达92%,可实现在一条线上生产四款车型的柔性化生产。同时,该车间拥有蓝光自动检测、激光在线检测等各种智能化检测手段,使得焊接精度控制在1.5毫米以内,在同行业处于领先水平。
当天下午5点,在历经约6个小时的焊接流程后,CS55PLUS的白车身进入到了涂装环节。
涂装车间除了拥有108台机器人以外,还采用了镜像车间智能技术,能够精确定位车辆实时位置,实时显示停线等信息,并能对车间关键质量指标数据进行统计分析。
此外,通过物联网技术,涂装车间每一个设备的“身体健康”情况也被巨细无遗地监控起来,从而能实现预防性维护、预测性维护。
由于涂装涉及漆面烘干、强冷等环节,耗时一般在8小时左右。
次日清晨5点 新车下线
第二天凌晨1点,记者来到汽车生产的最后一个环节——总装二车间,已经涂装完成的CS55PLUS车身被送到总装线上,由夜班继续接下来的生产。
比起前几个工艺环节,总装车间所展现的智能技术和应用更加有趣且繁多。
例如,在轮胎安装环节,记者看到,摄像头正对输送带上所有轮胎的胎皮花纹进行图像识别,总共20多种不同型号的汽车轮胎被自动区分开,输送往不同的工区。
在主胎的安装工区,工人正在操作一台自动拧紧螺丝的设备,该设备有5个孔轴,可同时拧紧一个轮胎上的5颗螺丝。总装二车间区域经理郭坤介绍,这台设备上有扭力传感装置,可以保证所有螺丝的扭力一致,如果出现扭力差异,生产线将立即报警,进行差错修正。这样能保证生产出来的汽车轮胎螺栓连接安全可靠,不会出现松动。
在车辆仪表台装配线上,摄像头对各种易混件全部进行外观检测,并扫描零部件上的件号进行匹配,确保零部件安装万无一失。
这样的智能化应用,在总装车间随处可见。而这所有的智能化功能,都被统合在长安汽车工厂的智慧运营平台中。据介绍,目前该工厂96%的设备都实现了联网,设备和人、系统实现了“彼此对话”。
基于智能化平台中的现场数据,长安汽车逐步建设起由后端拉动前端的生产模式。
记者在该厂的智慧运营平台上看到,各种即时生成的生产数据被用于自动排产、实时盘存,并形成精益生产模式。受总装车间后端需求拉动,该厂冲压车间实际库存量低至1.5天,优于合资车厂水平,并使得冲压车间盈利能力提升大约32.9%,减低运营成本14.1%。
8月11日清晨5点左右,一辆崭新的CS55PLUS通过最终检测环节,正式下线,在18个小时中完成了“从无到有”。
我市已累计实施4700多个智能化改造项目
重庆日报讯 (记者 白麟)8月10日,重庆日报记者从市经信委获悉,截至目前,全市已累计实施智能化改造项目4700多个,计划到今年底达到5000个,届时,我市将有80%以上的规上企业迈入数字化制造阶段,60%以上的规上企业迈入“数字化+网络化”制造阶段。
据了解,自2018年我市出台智能制造实施方案以来,全市企业掀起智能化改造浪潮。除了已累计实施4700多个智能化改造项目,我市还建成734个数字化车间和127个智能工厂,并且正推动建设584个网络化协同、个性化定制、服务化延伸等产业项目。
记者在蓝黛动力传动机械股份有限公司看到,企业数字化车间里,随处可见繁忙的机器人、飞速运转的自动化设备;在西南药业粉针剂智能化制药车间看到,一排排玻璃药瓶依次进入循环滚动的生产流水线,通过自动光电扫描、智能称重检漏设备,以前最费力的装箱、打包、码垛等操作工序,如今都由自动化装箱码垛系统来完成;在美心集团生产现场,只见工人按下生产线旁边的按钮,一块块木板就自动被送上滚动的履带,数十台机器人挥舞着机械臂,一扇扇精美的木门接连下线。
市经信委相关负责人告诉记者,如今,这样的智能生产场景,在我市制造业企业已属常态。这些实施智能化改造后的企业,运营成本平均降低15%以上,生产效率提高10%以上,产品不良品率降低10%以上,能源利用率提高8%以上。
重庆大学机械与运载工程学院教授郭钢:
智能化应贯通汽车产业的全过程
记者 白麟
作为国内重要的汽车制造基地,重庆应该如何全方位推动汽车产业智能化发展?重庆日报记者对此专访了重庆大学机械与运载工程学院教授郭钢。
郭钢认为,汽车产业的智能化应贯通汽车产业的全过程,也就是说,除了产品本身的智能化以外,车企还需要推动研发的智能化、生产以及配套的供应链管理智能化、市场营销的智能化。
在郭钢看来,上述几个方面需要应用整体思维、同步推进。例如,通过智能化手段设计高品质的智能汽车,除了要考虑整车到零部件功能、性能和用户体验的提升,还要同时面向制造进行设计。在设计的时候要考虑如何解决整车智能化的四大工艺实现。
同样,在智能化生产方面,也要从设计研发的角度考虑,对工艺进行相应的优化。比如冲压工艺,从过去单机智能化,到如今一条完整生产线的智能化,从而实现冲压、焊接、涂装、总装四大制造工艺的智能化,在很大程度上也是为了满足市场竞争和目标用户消费升级需求。
“要提升四大工艺的智能化程度,就必须提升设备的智能化。”郭钢表示,此外,基于数字化的设备互联互通,也是实现智能化的关键环节。